Proceso de producción del Acero
- procesosdfabricacion
- 19 feb 2016
- 23 Min. de lectura
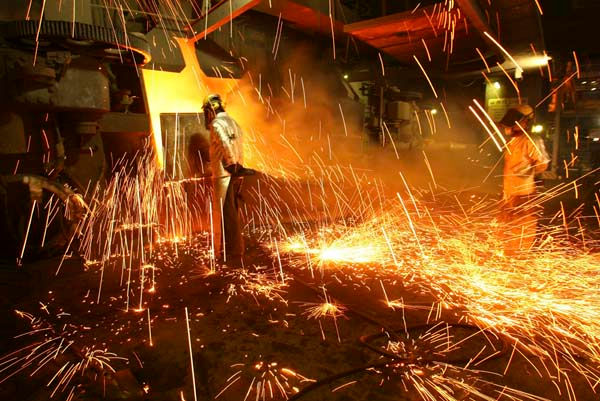
INSTITUTO TECNOLOGICO SUPERIOR
DE COMALCALCO
PROCESO DE PRODUCCIÓN DEL ACERO
PROFESOR: ING. JUAN CARLOS MARTÍNEZ
ROCHA.
ASIGNATURA: PROCESOS DE FABRICACION
INTEGRANTES DEL EQUIPO:
LUIS GUSTAVO OSORIO LÓPEZ
JOSÉ ALFREDO JIMÉNEZ JIMÉNEZ
CARLOS ANTONIO LEYVA MARTÍNEZ
HUGO SÁNCHEZ MAGAÑA
JORGE ALBERTO LEYVA GONZALES
HOMERO HERNÁNDEZ DE LA CRUZ
LUIS G. DE LA CRUZ CÓRDOVA
4° SEMESTRE GRUPO B
INDICE
Introducción……………………………………...…………………… 2
Objetivo……………………………………………………………….....3
Historia del acero……………………………………………………….4
Composición………………………………………………………........7
Características………………………………………………………….11
Proceso de producción……………………………………. ………....13
Usos y productos…………………………………………………….....22
Imágenes……………………………………………………………......26
Bibliografía…………………………………………..…………….........28
INTRODUCCIÓN
El acero es una aleación de hierro con carbono en una proporción que oscila entre 0,03 y 2%. Se suele componer de otros elementos, ya inmersos en el material del que se obtienen. Pero se le pueden añadir otros materiales para mejorar su dureza, maleabilidad u otras propiedades.
Las propiedades físicas de los aceros y su comportamiento a distintas temperaturas dependen sobre todo de la cantidad de carbono y de su distribución. Antes del tratamiento térmico, la mayoría de los aceros son una mezcla de tres sustancias, ferrita, perlita, cementita. La ferrita, blanda y dúctil, es hierro con pequeñas cantidades de carbono y otros elementos en disolución. La cementita es un compuesto de hierro con el 7% de carbono aproximadamente, es de gran dureza y muy quebradiza. La perlita es una mezcla de ferrita y cementita, con una composición específica y una estructura características, sus propiedades físicas con intermedias entre las de sus dos componentes. La resistencia y dureza de un acero que no ha sido tratado térmicamente depende de la proporciones de estos tres ingredientes. Cuanto mayor es el contenido en carbono de un acero, menor es la cantidad de ferrita y mayor la de perlita: cuando el acero tiene un 0,8% de carbono, está por compuesto de perlita. El acero con cantidades de carbono aún mayores es una mezcla de perlita y cementita.
OBJETIVO
El objetivo de este tema es darnos a conocer más que nada su composición química siendo utilizada para ciertos tipos de materiales tales como tubos de acero los cuales son utilizados las empresas por ejemplo se puede utilizar para transportar el gas el cual requiere ciertos tipos de máquinas para poder trabajar correctamente es así como damos un punto del cual importante saber sobre este material tan complejo y tan indispensable para los diferentes tipos de trabajos en este trabajo se describen cada una de sus características desde la historia del acero , el proceso de elaboración que se debe llevar, cuando ya esta el producto terminado y para que podemos utlizarlos
1. HISTORIA DEL ACERO
La fecha en que se descubrió la técnica de fundir el mineral de hierro no es conocida con exactitud. Los primeros artefactos encontrados por arqueólogos datan del año 3.000 A. de C. en Egipto.
Sin embargo, los griegos a través de un tratamiento térmico, endurecían armas de hierro hacia el 1.000 A. de C.
En realidad conseguían una especie de acero: el hierro absorbía carbono de las brasas y se formaba una “piel” de acero en la superficie. “200 A.C.: los indios, fabricantes de acero”. Hacia el 200 A.C., los artesanos de la India dominaban ya un método mejor para producir acero. Colocaban trozos de hierro carbonado o con “piel” de acero en un recipiente de arcilla cerrado, o crisol, y lo calentaban intensamente en un horno. El carbono se distribuía gradualmente a través del hierro y producía una forma de acero mucho más uniforme. “1740: redescubrimiento del acero al crisol”. En 1740, el inglés Benjamin Huntsman redescubrió el procedimiento indio por casualidad, al calentar una mezcla de hierro y una cantidad cuidadosamente medida de carbón vegetal en un crisol. Pese a la invención de otros procedimientos, siguió prefiriéndose el método del crisol para obtener acero de alta calidad, hasta que en 1902 se inventó el horno eléctrico.
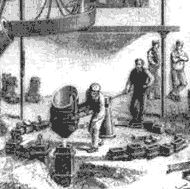
“1856: convertidor Bessemer”. En 1856, el inventor inglés Henry Bessemer patentó un método más barato para fabricar acero en gran escala. Un chorro de aire atravesaba el hierro fundido y quemaba todo el carbono necesario para obtener el acero. Bessemer construyó un recipiente cónico de acero forrado de ladrillos refractarios que se llamó convertidor y que se podía inclinar para vaciarlo. El hierro fundido se vertía en el convertidor situado en posición vertical, y se hacía pasar aire a través de orificios abiertos en la base. El “soplado”, que duraba unos veinte minutos, resultaba espectacular. El primer acero fabricado por este método era quebradizo por culpa del oxígeno absorbido.

“1864: horno de solera abierta”. El mismo año en que Bessemer presentó su procedimiento, los hermanos de origen alemán William y Friedrich Siemens estaban desarrollando un método para precalentar el aire inyectado a los hornos. A cada extremo del horno colocaron cámaras de ladrillos entrecruzados que se calentaban con los gases de la combustión y caldeaban después el aire que se inyectaba en el horno. Dos años más tarde, los hermanos Siemens patentaron un horno de solera para acero que incorporaba sus precalentadores o “regeneradores”. Pero no tuvo éxito hasta que lo mejoraron dos hermanos franceses, Pierre y Emile Martín, en 1864.
“1902: acero por arco eléctrico”. William Siemens había experimentado en 1878 con la electricidad para calentar los hornos de acero. Pero fue el metalúrgico francés Paul Héroult (coinventor del método moderno para fundir aluminio) quien inició en 1902 la producción comercial del acero en horno eléctrico. Se introduce en el horno chatarra de acero de composición conocida y se hace saltar un arco eléctrico entre la chatarra y grandes electrodos de carbono situados en el techo del horno.
“1948: proceso del oxígeno básico”. Tras la segunda guerra mundial se iniciaron experimentos en varios países con oxígeno puro en lugar de aire para los procesos de refinado del acero. El éxito se logró en Austria en 1948, cuando una fábrica de acero situada cerca de la ciudad de Linz y de Donawitz desarrolló el proceso del oxígeno básico o L-D.
“1950: fundición continua”. En el método tradicional de moldeo, el acero fundido del horno se vierte en moldes o lingotes y se deja enfriar. Luego se vuelven al calentar los lingotes hasta que se ablandan y pasan a trenes de laminado, donde se reducen a planchas de menor tamaño para tratamientos posteriores.
2. COMPOSICION
Aunque la composición química de cada fabricante de aceros es casi secreta, certificando a sus clientes solo la resistencia y dureza de los aceros que producen, sí se conocen los compuestos agregados y sus porcentajes admisibles para ciertos tipos de aplicaciones, ya sea que se quiera un acero más tenaz, duro, resistente al esfuerzo mecánico, etc.
A continuación un listado de los elementos aleantes mas importantes y el efecto que estos tiene en el producto final.
Níquel: una de las mayores ventajas que reporta el empleo del níquel, es evitar el crecimiento del grano en los tratamientos térmicos, lo que sirve para producir en ellos gran tenacidad. El níquel al ser un elemento gammágeno además hace descender los puntos críticos y por ello los tratamientos pueden hacerse a temperaturas ligeramente más bajas que la que corresponde a los aceros ordinarios.
Este elemento le da a los aceros un límite de elasticidad ligeramente más elevado y mayores alargamientos y resistencias que con los aceros al carbono o de baja aleación. En la actualidad se ha restringido mucho su empleo, pero sigue siendo un elemento de aleación indiscutible para los aceros de construcción empleados en la fabricación de piezas para máquinas y motores de gran responsabilidad, se destacan sobre todo en los aceros cromo-níquel y cromo-níquel-molibdeno.
El níquel es un elemento de extraordinaria importancia en la fabricación de aceros inoxidables y resistentes a altas temperaturas. Es el principal formador de austenita, que aumenta la tenacidad y resistencia al impacto.
Los aceros más utilizados al níquel son los siguientes:
Aceros cromo − níquel y cromo − níquel − molibdeno: Con porcentajes de níquel variables desde 1 a 5%: estos se emplean para cementación y con porcentajes de 0.25 a 0.40% de carbono se emplean para piezas de gran resistencia. En estos aceros los porcentajes de estos elementos aleados suelen estar en la relación aproximada de 1% de cromo y 3% de níquel.
Aceros de media aleación níquel − molibdeno y níquel − manganeso: Se suelen emplear para piezas de gran resistencia y para piezas cementadas con porcentajes de carbono variables de 0.25 a 0.40% en el primer caso y de 0.10 a 0.25% en el segundo, variando el contenido en níquel de 1 a 2%, el de manganeso de 1 a 1.5% y el del molibdeno de 0.15 a 0.40%.
Aceros inoxidables y resistentes al calor cromo − níqueles: con 8 a 20% de níquel que son de estructura austenítica.
Otros aceros de menor importancia son los aceros cromo - níqueles para estampación en caliente.
Cromo: es uno de los elementos especiales más empleados para la fabricación de aceros aleados, usándose indistintamente en los aceros de construcción, en los de herramientas, en los inoxidables y los de resistencia en caliente. Se emplea en cantidades diversas desde 0.30% a 30% según los casos y sirve para aumentar la dureza y la resistencia a la tracción de los aceros, mejora la templabilidad, impide las deformaciones en el temple, aumenta la resistencia al desgaste y la inoxidabilidad. Forma carburos muy duros y brinda al acero mayor dureza, resistencia y tenacidad a cualquier temperatura. Solo o aleado con otros elementos, proporciona a los aceros características de inoxidables y refractarios. También se utiliza en revestimientos embellecedores o recubrimientos duros de gran resistencia al desgaste, como émbolos, ejes, etc.
Molibdeno: es un elemento habitual del acero y aumenta mucho la profundidad de endurecimiento de acero, así como su tenacidad. Los aceros inoxidables austeníticos contienen molibdeno para mejorar la resistencia a la corrosión.
El molibdeno en combinación con cromo, es muy efectivo en la estabilización de una película pasiva en presencia cloruros. Es efectivo en la prevención grietas o picaduras por corrosión. El Molibdeno junto al cromo provee la más grande resistencia a la corrosión en los aceros inoxidables.
Wolframio (Tungsteno): Forma con el hierro carburos muy complejos, estables y durísimos, evitando que se desafilen o ablanden las herramientas. En porcentajes del 14 al 18 %, proporciona aceros rápidos con los que es posible triplicar la velocidad de corte de los aceros al carbono para herramientas. También se usa para la fabricación de aceros para imanes.
Todos los aceros herramienta aleados con Wolframio poseen una resistencia muy alta a la temperatura.
Vanadio: posee una enérgica acción desoxidante y forma carburos complejos con el hierro que proporcionan al acero una buena resistencia a la fatiga, tracción y poder cortante en los aceros para herramientas. Además de que brinda al acero una resistencia al ablandamiento por revenido.Básicamente es utilizado para eso, para aceros tipo herramienta.
Manganeso: aparece prácticamente en todos los aceros, debido principalmente a que se añade como elemento de aleación para neutralizar la perniciosa influencia del azufre y del oxigeno, que siempre suelen contener los aceros cuando se encuentran en estado líquido en los hornos durante los procesos de fabricación. También actúa como desoxidante y evita, en parte, que en la solidificación del acero que se desprendan gases que den lugar a porosidades perjudiciales en el material.
Si los aceros no tuvieran manganeso, no se podrían laminar ni forjar, porque el azufre que suele encontrarse en mayor o menor cantidad en los aceros, formarían sulfuros de hierro, que son cuerpos de muy bajo punto de fusión (981ºC aproximadamente) que a las temperaturas de trabajo en caliente (forja o laminación) funden, y al encontrarse contorneando los granos de acero crean zonas de debilidad y las piezas y barras se abren en esas operaciones de transformación. Los aceros ordinarios y los aceros aleados en los que el manganeso no es elemento fundamental, suelen contener generalmente porcentajes de manganeso variables de 0.30 a 0.80%.
El Manganeso en porcentajes mayores a 11% hace austenítico al acero.
Silicio: aumenta la resistencia de los aceros bajos en carbono y, a su vez, aumenta moderadamente la templabilidad. Se usa como el principal elemento desoxidante, incluso por encima del manganeso.
Cobalto: elemento de aleación endurecedor. Disminuye la templabilidad. Mejora la dureza en caliente. Se usa en los aceros rápidos y aceros refractarios. Aumenta las propiedades magnéticas de los aceros.
Aluminio: elemento utilizado para afinar el grano. Se emplea también como elemento de aleación en los aceros de nitruración, que suele tener 1% aproximadamente de aluminio. Como desoxidante se suele emplear frecuentemente en la fabricación de muchos aceros. Todos los aceros aleados en calidad contienen aluminio en porcentajes pequeñísimos, variables generalmente desde 0.001 a 0.008%.
Titanio: Se suelen añadir pequeñas cantidades de titanio a algunos aceros muy especiales para desoxidar y afinar el grano. El titanio tiene gran tendencia a formar carburos y a combinarse con el nitrógeno.
Cobre: El cobre se suele emplear para mejorar la resistencia a la corrosión de ciertos aceros de 0,15 a 0,30 % de carbono, que se usan para grandes construcciones metálicas.
Boro: El boro es un elemento de aleación que ha comenzado a ser empleado muy recientemente. Se ha visto que cantidades pequeñísimas de boro mejoran notablemente la templabilidad. Además logra aumentar la capacidad de endurecimiento cuando el acero está totalmente desoxidado.
Estaño: es el elemento que se utiliza para recubrir láminas muy delgadas de acero que conforman la hojalata.
Nitrógeno: se agrega a algunos aceros para promover la formación de austenita.
Plomo: el plomo no se combina con el acero, se encuentra en él en forma de pequeñísimos glóbulos, como si estuviese emulsionado, lo que favorece la fácil mecanización por arranque de viruta, (torneado, cepillado, taladrado, etc.) ya que el plomo es un buen lubricante de corte, el porcentaje oscila entre 0.15 y 0.30 % debiendo limitarse el contenido de carbono a valores inferiores al 0.5 % debido a que dificulta el templado y disminuye la tenacidad en caliente.

3. CARACTERISTICAS
El acero es una aleación de hierro y carbono (máximo 2.11% de carbono), al cual se le adicionan variados elementos de aleación, los cuales le confieren propiedades mecánicas específicas para su diferente utilización en la industria. Los principales elementos de aleación son: Cromo, Tungsteno, Manganeso, Níquel, Vanadio, Cobalto, Molibdeno, Cobre, Azufre y Fósforo. Los productos ferrosos con más de 2.11% de carbono denominan fundiciones de hierro. O Elementos de Aleación Carbono: Es el elemento que tiene más influencia en el comportamiento del acero; al aumentar el porcentaje de carbono, mejora la resistencia mecánica, la Templabilidad y disminuye la ductilidad.
Boro: El Boro que se encuentra en el acero proviene exclusivamente de las adiciones voluntarias de este elemento en el curso de su fabricación. Ejerce una gran influencia sobre la templabilidad del acero, bastando porcentajes muy pequeños, a partir de 0.0004%, para aumentarla notablemente.
Azufre: Aumenta la Maquinabilidad, ya que forma inclusiones no metálicas llamadas sulfuros de magnesio, discontinuidades en la matriz metálica que favorecen la formación de viruta corta.
Cromo: Es un gran formador de carburos, aumenta la dureza y la resistencia al desgaste, y solo reduce la ductilidad. Mejora la resistencia a la alta temperatura y a la formación de cascarilla. En cantidades mayores al 12%, hace al acero resistente a la corrosión.
Fósforo: Incrementa la resistencia y reduce la ductilidad de la ferrita. Aumenta la brillantez. Este elemento, en cantidades superiores al 0.004%, disminuye todas las propiedades mecánicas del acero.
Molibdeno: Formador de carburos, reduce el crecimiento del grano, mejora la resistencia al desgaste y la capacidad de conservar la dureza a temperaturas altas.
Cobalto: Elemento que desplaza las curvas TTT hacia la izquierda, aumentando la velocidad crítica y disminuyendo la templabilidad. Aumenta la dureza, y asociado al níquel o al cromo, forman aceros de débil coeficiente de dilatación, cercano al vidrio. Aumenta la velocidad crítica de enfriamiento y en los aceros para trabajo en caliente y rápidos incrementa la disipación de temperatura.
Manganeso: Mejora la resistencia a la tracción y al desgaste, tiene buena influencia en la forja, la soldadura y la profundidad de temple. Facilita el mecanizado.
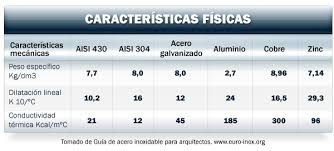

4. PROCESO DE PRODUCCION
A la fabricación del acero se destina aproximadamente el 75% del arrabio que se produce en los altos hornos. El acero es una aleación de hierro con una pequeña cantidad de carbono (siempre menor al 1,76%).
El acero se puede obtener a partir de dos materias primas fundamentales:
• El arrabio, obtenido a partir de mineral en instalaciones dotadas de alto horno (proceso integral);
• Las chatarras, tanto férricas como inoxidables,
El tipo de materia prima condiciona el proceso de fabricación. En líneas generales, para fabricar acero a partir de arrabio se utiliza el convertidor con oxígeno, mientras que partiendo de chatarra como única materia prima se utiliza exclusivamente el horno de arco eléctrico (proceso electro-siderúrgico). Los procesos en horno de arco eléctrico pueden usar casi un 100% de chatarra metálica como primera materia [Steel Recycling Institute; 2000], convirtiéndolo en un proceso más favorable desde un punto de vista ecológico. Aun así, la media de las estadísticas actuales calcula que el 85% de las materias primas utilizadas en los hornos de arco eléctrico son chatarra metálica [Wolf, B.; et al; 2001].
Las estimaciones del porcentaje mundial de industrias que utilizan el convertidor con oxígeno en 1995 eran del 59% y de un 33% para las que utilizaban horno de arco eléctrico [Wolf, B.; et al; 2001].
4.1. Fabricación del acero en el horno convertidor con oxigeno
El acero se obtiene en el horno convertidor a través de una operación que se denomina afino, uno de los métodos más empleados para realizar el afino es el sistema de inyección de oxígeno (LD). Este sistema consiste en lo siguiente:
¿Qué metemos en el convertidor?
a) Arrabio: Nada más sacarlo del alto horno (antes de que se enfríe) ya se mete en el convertidor. Recordamos que el arrabio tiene hierro, carbón e impurezas.
b) Chatarra de hierro: Procedente de coches, electrodomésticos,...
c) Fundente: Recordamos que es carbonato cálcico y que lo empleamos como detergente para eliminar las impurezas.
d) Oxigeno: Se inyecta a presión en el centro del convertidor a través de tubo con forma de lanza, y con ello conseguimos quemar parte del carbón que no se había quemado en el alto horno.
¿Que obtenemos del convertidor?
a) Escorias: El fundente se pega a las impurezas y las hace flotar formando la escoria.
b) Acero: En la parte inferior del convertidor quedará el hierro y el carbón que no se ha quemado.
Finalmente iniciamos el proceso de colada, para ello inclinamos parcialmente el convertidor para que caiga solo la escoria (como cuando tratamos de eliminar solo la nata que queda encima de un vaso de leche). Una vez eliminada la escoria se vuelca totalmente el convertidor para que caiga el acero dentro de los moldes que tendrán la forma de las piezas que queremos obtener.

Los aceros se pueden mezclar con otros elementos químicos (silicio, cromo, níquel, manganeso,....) para obtener aceros aleados, pudiendo obtener en función del elemento con el que juntemos y su cantidad podemos obtener acero con múltiples propiedades y para múltiples aplicaciones. Esto no ocurre así para las fundiciones.
Por ejemplo, el acero mezclado con cromo se vuelve inoxidable o si le añadimos wolframio evitamos que se ablande cuando se calienta demasiado.
4.2. Fabricación del acero en el horno eléctrico
Las aleaciones de acero se realizan generalmente a través del horno de arco eléctrico, incluyendo el acero inoxidable. En algunos tipos de acero inoxidable se añade a su composición molibdeno, titanio, niobio u otro elemento con el fin de conferir a los aceros distintas propiedades.
Tras el proceso de reconversión industrial de la siderurgia en España se abandonó la vía del alto horno y se apostó de forma decidida por la obtención de acero a través de horno eléctrico. En este proceso, la materia prima es la chatarra, a la que se le presta una especial atención, con el fin de obtener un elevado grado de calidad de la misma. Para ello, la chatarra es sometida a unos severos controles e inspecciones por parte del fabricante de acero, tanto en su lugar de origen como en el momento de la recepción del material en fábrica. La calidad de la chatarra depende de tres factores:
[endif]--Su facilidad para ser cargada en el horno - Su comportamiento de fusión (densidad de la chatarra, tamaño, espesor, forma)
Su composición, siendo fundamental la presencia de elementos residuales que sean difíciles de eliminar en el proceso del horno
Atendiendo a su procedencia, la chatarra se puede clasificar en tres grandes grupos:
a) Chatarra reciclada: formada por despuntes, rechazos, etc. originados en la propia fábrica. Se trata de una chatarra de excelente calidad.
b) Chatarra de transformación: producida durante la fabricación de piezas y componentes de acero (virutas de máquinas herramientas, recortes de prensas y guillotinas, etc.).
c) Chatarra de recuperación: suele ser la mayor parte de la chatarra que se emplea en la acería y procede del desguace de edificios con estructura de acero, plantas industriales, barcos, automóviles, electrodomésticos, etc.
La fabricación del acero en horno eléctrico se basa en la fusión de las chatarras por medio de una corriente eléctrica, y al afino posterior del baño fundido.
El horno eléctrico consiste en un gran recipiente cilíndrico de chapa gruesa (15 a 30 mm de espesor) forrado de material refractario que forma la solera y alberga el baño de acero líquido y escoria. El resto del horno está formado por paneles refrigerados por agua. La bóveda es desplazable para permitir la carga de la chatarra a través de unas cestas adecuadas.
La bóveda está dotada de una serie de orificios por los que se introducen los electrodos, generalmente tres, que son gruesas barras de grafito de hasta 700 mm de diámetro. Los electrodos se desplazan de forma que se puede regular su distancia a la carga a medida que se van consumiendo.
Los electrodos están conectados a un transformador que proporciona unas condiciones de voltaje e intensidad adecuadas para hacer saltar el arco, con intensidad variable, en función de la fase de operación del horno.
Otro orificio practicado en la bóveda permite la captación de los gases de combustión, que son depurados convenientemente para evitar contaminar la atmósfera. El horno va montado sobre una estructura oscilante que le permite bascular para proceder al sangrado de la escoria y el vaciado del baño.
El proceso de fabricación se divide básicamente en dos fases: la fase de fusión y la fase de afino.
4.2.1. Fase de fusión
Una vez introducida la chatarra en el horno y los agentes reactivos y escorificantes (principalmente cal) se desplaza la bóveda hasta cerrar el horno y se bajan los electrodos hasta la distancia apropiada, haciéndose saltar el arco hasta fundir completamente los materiales cargados. El proceso se repite hasta completar la capacidad del horno, constituyendo este acero una colada.
4.2.2. Fase de afino
El afino se lleva a cabo en dos etapas. La primera en el propio horno y la segunda en un horno cuchara. En el primer afino se analiza la composición del baño fundido y se procede a la eliminación de impurezas y elementos indeseables (silicio, manganeso, fósforo, etc.) y realizar un primer ajuste de la composición química por medio de la adición de ferroaleaciones que contienen los elementos necesarios (cromo, níquel, molibdeno, vanadio o titanio).
El acero obtenido se vacía en una cuchara de colada, revestida de material refractario, que hace la función de cuba de un segundo horno de afino en el que termina de ajustarse la composición del acero y de dársele la temperatura adecuada para la siguiente fase en el proceso de fabricación.
4.2.3. La colada continúa
Finalizado el afino, la cuchara de colada se lleva hasta la artesa receptora de la colada continua donde vacía su contenido en una artesa receptora dispuesta al efecto.
La colada continua es un procedimiento siderúrgico en el que el acero se vierte directamente en un molde de fondo desplazable, cuya sección transversal tiene la forma geométrica del semiproducto que se desea fabricar; en este caso la palanquilla.
La artesa receptora tiene un orificio de fondo, o buza, por el que distribuye el acero líquido en varias líneas de colada, cada una de las cuales disponen de su lingotera o molde, generalmente de cobre y paredes huecas para permitir su refrigeración con agua, que sirve para dar forma al producto. Durante el proceso la lingotera se mueve alternativamente hacia arriba y hacia abajo, con el fin de despegar la costra sólida que se va formando durante el enfriamiento.
Posteriormente se aplica un sistema de enfriamiento controlado por medio de duchas de agua fría primero, y al aire después, cortándose el semiproducto en las longitudes deseadas mediante sopletes que se desplazan durante el corte.
En todo momento el semiproducto se encuentra en movimiento continuo gracias a los rodillos de arrastre dispuestos a los largo de todo el sistema.
Finalmente, se identifican todas las palanquillas con el número de referencia de la colada a la que pertenecen, como parte del sistema implantado para determinar la trazabilidad del producto, vigilándose la cuadratura de su sección, la sanidad interna, la ausencia de defectos externos y la longitud obtenida.
4.2.4. La laminación
Las palanquillas no son utilizables directamente, debiendo transformarse en productos comerciales por medio de la laminación o forja en caliente.
De forma simple, podríamos describir la laminación como un proceso en el que se hace pasar al semiproducto (palanquilla) entre dos rodillos o cilindros, que giran a la misma velocidad y en sentidos contrarios, reduciendo su sección transversal gracias a la presión ejercida por éstos. En este proceso se aprovecha la ductilidad del acero, es decir, su capacidad de deformarse, tanto mayor cuanto mayor es su temperatura. De ahí que la laminación en caliente se realice a temperaturas comprendidas entre 1.250ºC, al inicio del proceso, y 800ºC al final del mismo.
La laminación sólo permite obtener productos de sección constante, como es el caso de las barras corrugadas.
El proceso comienza elevando la temperatura de las palanquillas mediante hornos de recalentamiento hasta un valor óptimo para ser introducidas en el tren de laminación. Generalmente estos hornos son de gas y en ellos se distinguen tres zonas: de precalentamiento, de calentamiento y de homogeneización. El paso de las palanquillas de una zona a otra se realiza por medio de distintos dispositivos de avance. La atmósfera en el interior del horno es oxidante, con el fin de reducir al máximo la formación de cascarilla.
Alcanzada la temperatura deseada en toda la masa de la palanquilla, ésta es conducida a través de un camino de rodillos hasta el tren de laminación. Este tren está formado por parejas de cilindros que van reduciendo la sección de la palanquilla. Primero de la forma cuadrada a forma de óvalo, y después de forma de óvalo a forma redonda. A medida que disminuye la sección, aumenta la longitud del producto transformado y, por tanto, la velocidad de laminación. El tren se controla de forma automática, de forma que la velocidad de las distintas cajas que lo componen va aumentando en la misma proporción en la que se redujo la sección en la anterior.
El tren de laminación se divide en tres partes:
Tren de desbaste: donde la palanquilla sufre una primera pasada muy ligera para romper y eliminar la posible capa de cascarilla formada durante su permanencia en el horno.
Tren intermedio: formado por distintas cajas en las que se va conformando por medio de sucesivas pasadas la sección.
Tren acabador: donde el producto experimenta su última pasada y obtiene su geometría de corrugado.
Las barras ya laminadas se depositan en una gran placa o lecho de enfriamiento. De ahí, son trasladadas a las líneas de corte a medida y empaquetado y posteriormente pasan a la zona de almacenamiento y expedición.
En el caso de la laminación de rollos, éstos salen del tren acabador en forma de espira, siendo transportados por una cinta enfriadora, desde la que las espiras van siendo depositadas en un huso, donde se compacta y se ata para su expedición, o bien se lleva a una zona de en carretado, dónde se forman bobinas en carrete.
Durante la laminación se controlan los distintos parámetros que determinarán la calidad del producto final: la temperatura inicial de las palanquillas, el grado de deformación de cada pasada —para evitar que una deformación excesiva dé lugar a roturas o agrietamientos del material—, así como el grado de reducción final, que define el grado de forja, y sobre todo el sistema de enfriamiento controlado.
4.3. Flujos de materia del proceso de fabricación del acero
Para producir una tonelada de acero virgen se necesitan 1500kg de ganga de hierro, 225kg de piedra caliza y 750kg de carbón (en forma de coque) [Lawson, B.; 1996]
La obtención del acero pasa por la eliminación de las impurezas que se encuentran en el arrabio o en las chatarras, y por el control, dentro de unos límites especificados según el tipo de acero, de los contenidos de los elementos que influyen en sus propiedades.
Las reacciones químicas que se producen durante el proceso de fabricación del acero requieren temperaturas superiores a los 1000ºC para poder eliminar las sustancias perjudiciales, bien en forma gaseosa o bien trasladándolas del baño a la escoria.

4.4. Opciones de reciclado del acero.
Al ser un material de alta intensidad energética, el acero tiene un alto potencial para ser reciclado. El acero, se puede reciclar técnicamente un número indefinido de veces, casi sin degradación en la calidad.
Aun así, la oxidación reduce la cantidad de material no oxidado. Mientras que prácticamente el 100% de los desechos de acero podrían ser re-introducidos en la industria, el porcentaje de acero reciclado se estima del 46%. Considerando la relativa facilidad con la que el acero puede ser reciclado y las ventajas obtenidas cuando se utiliza acero reciclado (requiere cuatro veces más energía producir acero de mineral virgen que reciclarlo [Green Networld, 1999]), resulta claro que hay muchas posibilidades de mejora. Las propiedades metálicas del acero son ventajosas ya que permiten que la separación del acero sea físicamente viable tanto en flujos de desecho como en plantas de construcción o demolición usando imanes para separar el metal del resto de residuos. La naturaleza magnética de los metales férricos facilita la separación y manejo durante el reciclado. Además, la escoria generada en el proceso de producción del acero, también puede ser reciclada, y se usa actualmente como sustituto de cemento o áridos en la construcción de carreteras y muros. Esta utilización es enormemente beneficiosa debido, por un lado, a la significativa reducción en la emisión de dióxido de carbono que de otra forma seria generado debido a la calcinación del mineral calcáreo, y por otro lado, a la reducción de escoria residual. Se estima que la creación de una tonelada de escoria (durante la producción de 3,5 toneladas de metal fundido) ahorra entre 3 y 5 GJ de energía y puede evitar la cocción de 1000 kg de calcárea, que tiene el potencial de generar entre 900 y 1200 kg de dióxido de carbono [Emi, T.; Seetharaman, S.; 2000].

5. USOS Y PRODUCTOS
El acero se usa para la fabricación de herramientas, utensilios, equipos mecánicos, partes de electrodomésticos y maquinas industriales. El acero se consume en la construcción de camiones y de maquinaria para la agricultura.
Las construcciones ferroviarias, ya sea de vías o material rodantes, consumen grandes cantidades de acero. Se puede encontrar este elemento en la industria de las armas, sobre todo en el armamento pesado, vehículos blindados y acorazados. Los astilleros que construyen barcos petroleros, gasistas y buques cisternas son grandes consumidores del acero.
Otra industria que recurre mucho acero es la automotriz, ya que muchas partes de los automóviles están compuestas por ese material, por ejemplo: el cigüeñal, piñones, ejes de transmisión de caja de velocidades y brazos de articulación de la dirección.
En la vida cotidiana encontramos el acero en envases como latas de conservas o bebidas, o bidones para pinturas, grasas o solventes.
También es un elemento importante que se utiliza para las estructuras de viviendas comunes y en gran parte de los edificios modernos. Es utilizado para armar el hormigón, reforzar los cimientos, transportar agua o gas. Es fundamental para formar el armazón de los edificios, además es utilizado como revestimiento en fachadas y techos.
Uso y ventajas del acero
El mundo moderno está construido con la fortaleza del acero, cuyas características han permitido concretar las ideas arquitectónicas y las obras civiles más ambiciosas y complejos imaginadas por el hombre. En ese sentido, el acero ofrece varias ventajas sobre otros materiales para la construcción, en principio por una mayor relación de resistencia y rigidez por unidad de volumen; además de ser un material homogéneo y que mantiene uniformidad de las propiedades mecánicas y físicas en el transcurso del tiempo. Tiene además la ventaja de manejabilidad de los componentes estructurales en taller y campo, facilidad de transporte, así como ligereza, ductilidad, resistencia a la fatiga y gran capacidad de absorción de energía. En el aspecto económico, por su menor peso, se obtiene un ahorro en la cimentación y por su alta relación resistencia/peso se usa de manera intensiva en edificios altos y estructuras de grandes claros. En un territorio como el de México, que se caracteriza por tener zonas sísmicas de gran riesgo, la construcción con acero ha demostrado un comportamiento altamente satisfactorio ante esos fenómenos naturales por la ductilidad que caracteriza al material siderúrgico. En términos de espacio útil, el acero representa una gran eficiencia constructiva al permitir claros más grandes que con la construcción tradicional de concreto armado. A la vez, las menores dimensiones de los miembros estructurales de acero respecto a las secciones de concreto permiten un uso eficiente del espacio. Esa característica, que da flexibilidad a los proyectos arquitectónicos, es también uno de los factores por los cuales los arquitectos se deciden por el uso del acero, que se adapta al trazado de grandes claros, vigas voladas, paredes oblicuas, aberturas en el piso y otros diseños especiales. Adicionalmente, la construcción con acero da la facilidad para hacer modificaciones, pues permite cambios de diseño para incorporar ascensores, escaleras y otros requerimientos mecánicos o arquitectónicos, y en obras terminadas las estructuras de acero pueden reforzarse para soportar cargas adicionales. La rapidez constructiva es otra ventaja a favor de la construcción con acero, material que permite realizar trabajos de prefabricación que facilitan ampliamente en tiempos la etapa de montaje estructural. En lo referente a los acabados existe una mayor economía y la estructura de acero es compatible con una gran variedad de materiales complementarios, con un menor costo.
La rapidez constructiva es otra ventaja a favor de la construcción con acero, material que permite realizar trabajos de prefabricación que facilitan ampliamente en tiempos la etapa de montaje estructural. En lo referente a los acabados existe una mayor economía y la estructura de acero es compatible con una gran variedad de materiales complementarios, con un menor costo. A todo ello, se suma una característica que es fundamental dentro de la mentalidad ambientalista de hoy: el acero es un material ecológico, 100 por ciento reciclable.
Vigas reticuladas permiten cubrir grandes luces: • Construcciones a realizar en tiempos reducidos de ejecución. • Construcciones en zonas muy congestionadas como centros urbanos o industriales en los que se prevean accesos y acopios dificultosos. • Edificios con probabilidad de crecimiento y cambios de función o de cargas. • Edificios en terrenos deficientes donde son previsibles asientos diferenciales apreciables; en estos casos se prefiere los entramados con nudos articulados. • Construcciones donde existen grandes espacios libres, por ejemplo: locales públicos, salones.
PROCESOS DE ACABADO
Existen distintos tipos de acabados para el acero, por lo tanto tiene una salida al mercado de gran variedad de formas y de tamaños, como varillas, tubos, raíles de ferrocarril o perfiles en H o en T. Estas formas se obtienen en las instalaciones siderúrgicas laminado los lingotes calientes o modelándolos de algún otro modo. El acabado del acero mejora también su calidad al refinar su estructura cristalina y aumentar su resistencia.
El método principal de trabajar el acero se conoce como laminado en caliente. En este proceso, el lingote colado se calienta al rojo vivo en un horno denominado foso de termodifusión y a continuación se hace pasar entre una serie de rodillos metálicos colocados en pares que lo aplastan hasta darle la forma y tamaño deseados. La distancia entre los rodillos va disminuyendo a medida que se reduce el espesor del acero.




BIBLIOGRAFIA
Manufactura, ingeniería y tecnología. Volumen 1 tecnologia xde materiales
Autor: Serope kalpakjian Steven R. Schmid
Séptima edición
Person, Mexico, 2014
Introduccion a los procesos de manufactura
Autor: Mikell P. Groover
Cuarta edicion
Mc Graw hill
La ciencia desde México
Autor: Lorenzo Martínez Gómez
Segunda edición
Person, Mexico
![endif]--
Comments